01
NANJING SPAREProducts Infomation
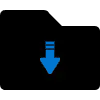
Download
Chemical media | Max. Temperature Resistance (Degree Celsius) | |||
Concentration % | Vinyl | m-Benzene | o-Phenylene | |
Hydrochloric acid | 30 | 82 | 65 | Not recommended |
Nitric acid | 35 | 38 | Not recommended | Not recommended |
Sulfuric acid | 25 | 82 | 65 | Not recommended |
Hydrofluoric acid | 10 | twenty four | Not recommended | Not recommended |
Lactic acid | 100 | 82 | 65 | 60 |
Hypochlorite | Saturated | 60 | Not recommended | Not recommended |
Trisodium phosphate | 50 | 82 | Not recommended | Not recommended |
Citric acid | All | 49 | Not recommended | Not recommended |
Potassium hydroxide | 10 | 49 | Not recommended | Not recommended |
Sodium hydroxide | 10 | 82 | Not recommended | Not recommended |
Calcium hydroxide | 25 | 82 | 65 | Not recommended |
Calcium hypochlorite | 25 | 82 | 65 | Not recommended |
Ferric chloride | 100 | 82 | 65 | 60 |
Aluminum chloride | All | 82 | 65 | 60 |
Mercury chloride | 100 | 82 | 65 | 60 |
Silver nitrate | 100 | 82 | 65 | 60 |
Fuel | All | 38 | 38 | 38 |
Ammonium salts | All | twenty four | Not recommended | Not recommended |
Copper oxide | Glycerin | 52 | 52 | Not recommended |
Sodium salt | All | twenty four | Not recommended | Not recommended |
Zinc chloride | All | twenty four | twenty four | Not recommended |
Acetone | 100 | 124 | Not recommended | Not recommended |
chloroform | 100 | Not recommended | Not recommended | Not recommended |
Copper salt | All | 82 | 65 | 60 |
Phenols | 10 | twenty four | Not recommended | Not recommended |
Ozone for water treatment | All | 38 | 38 | 38 |
Bleaching solution (for paper mills) | All | 82 | Not recommended | Not recommended |
Ammonia hydroxide | 30 | twenty four | Not recommended | Not recommended |
Paper mill black liquor | All | 82 | Not recommended | Not recommended |
All | 100 | 82 | 65 | 60 |
Sulfur Dioxide | Saturated | 82 | 65 | 60 |
Water | 100 | 82 | 65 | 60 |
Alum | All | 82 | 65 | 60 |
Chlorine water | Saturated | 49 | Not recommended | Not recommended |
NANJING SPAREProgressing

Fibres Roving+Fibre Guides
● Fiber reinforcements are precisely set-up and connected to mechanical pulling equipment.
Resin Bath
● Polymer resin in liquid form is pumped into a bath staged after the fiber reinforcement set-up.
● Process begins with reinforcing fibers being mechanically pulled through the resin bath where fibers are thoroughly saturated and impregnated with polymer resin.
Heating Die
● The saturated fibers are then pulled through a machined-precision die with entry portal and internal cavity in the shape of the final product. The composite is formed and cured within the heated, steel die.
Pullers
● Upon exiting the die, the thermoset composite is cut to the desired length and is a finished part.
Bonding | Tape connection or glue connection |
Connection method | Bolting |
Riveting | |
Fasteners |